Common Laboratory Safety Issues
Several safety issues and activities have been identified through inspections. The list below is intended to bring common issues to the attention of lab supervisors.
- Storage of combustible materials near the ceiling
- Storage of corrosive, flammable, or toxic chemicals above face height
- Incomplete/improper labeling of liquid waste containers
- Poor labeling of stock solutions or secondary containers
- Faded labels or label falling off
- Degraded plastic chemical containers
- Improper Protective Apparel
Incidents at Other Institutions
Storage of combustible materials near the ceiling
- The BC Fire Code indicates that the distance between top of storage and sprinkler height can be no less than 450mm (18 inches).
- Recommendation--remove items from the top of cabinets, lower shelves to increase space between stored materials and ceiling height.
Storage of corrosive, flammable, or toxic chemicals above face height
- If hazardous materials are stored or handled about face height, users must wear additional PPE, such as a face shield, in case the container is dropped of breaks.
- Recommendation--storage hazardous materials in dedicated cabinets, store non-hazardous materials (sodium chloride) the location instead.
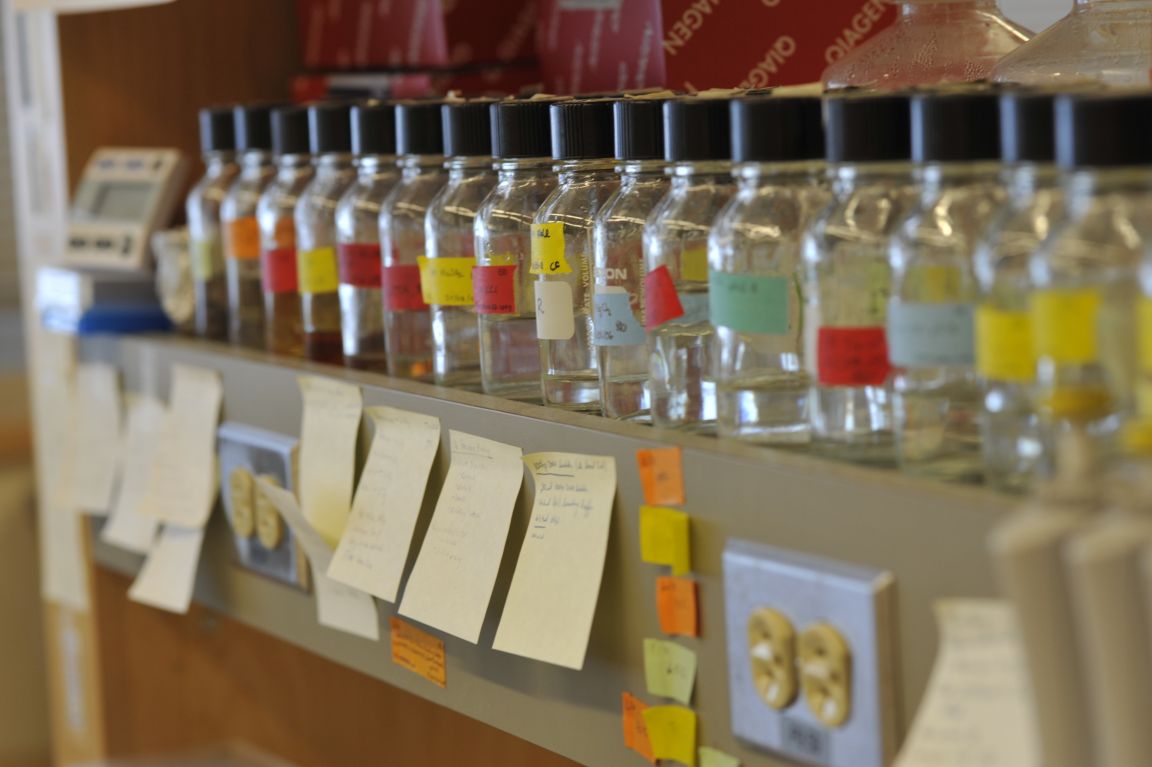
Storage of corrosive, flammable, or toxic chemicals above face height
Incomplete/improper labeling of liquid waste containers
- Waste containers are labeled as described in the Chemical Safety & Methodology Manual. The concentration and volume of liquid must be added to container label before the waste is added to the container. The label must be checked to ensure that the new waste is compatible with the wastes already inside the container. This information will be used for clean up, decontamination, or first aid treatment in case the container breaks or someone is exposed to the waste.
- The lab's Principal Investigator is responsible for ensuring that laboratory users complete waste tags.accurately.
- Recommendation--ensure all laboratory users are aware of UNBC waste handling procedures, provide continued supervision.
Poor labeling of stock solutions or secondary containers
- All chemicals located in a laboratory must be labeled with an identifier if they will not be used immediately or will be out of the immediate control of the user.
- Recommendation--define specific requirements for labeling of solutions and containers, enforce labeling requirements.
Faded labels or label falling off
- Containers are regularly found that are either missing a label or with labels that are damaged (ie., faded, corroded, torn). Labeling of chemical containers is part of right to know legislation and required by law. An annual checking of chemicals and prompt replacement of damaged labels when identified helps to address this issue. Although lab tape is commonly used for labeling, it is not intended as a long-term labeling solution because the glue hardens and the tape falls off if left for more than three years.
- The lab's Principal Investigator is responsible for ensuring that labels are complete and updated. Chemical containers that are found without labels during lab inspections or the annual chemical inventory are brought to the attention of the PI to be addressed.
- Recommendation--replace damaged labels, inspect containers every six months.
Degraded plastic chemical containers
- Over time supplied chemical containers degrade from combination of internal stresses, UV, temperature fluctuation, and chemical activity. Plastic containers and lids gradually become less flexible and can break unexpectedly, often in the users hand, causing chemical exposure and loss of the chemical. Annual checking of containers by gently squeezing plastic containers by gently flexing the plastic helps to identify degraded containers and provides an opportunity to transfer the chemical to a new container.
- Degraded chemical container that identified during lab inspections or the annual chemical inventory are brought to the attention of the PI to be addressed.
- Recommendation--inspect containers every 12 months for deterioration, check manufacturers guidelines for chemical and physical resistance.
- Students or supervisor do not wear protective equipment to match the activities occurring in the lab (e.g., wearing prescription glasses instead of safety glasses, not wearing gloves, wearing shorts or sandals).