Passive House, Active Research
The Wood Innovation Research Lab achieved the prestigious Passive House certification for energy efficiency
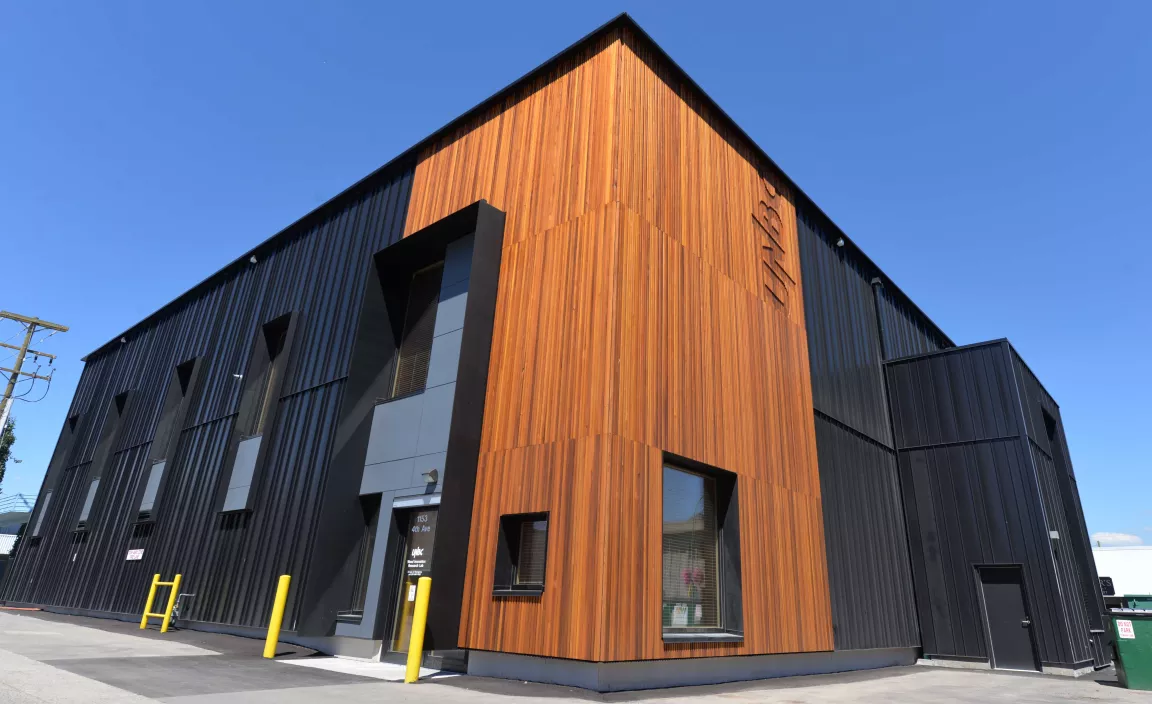
Building an ultra-energy efficient industrial-style building in a northern climate is no easy task, but the Wood Innovation Research Laboratory (WIRL) stands as proof it can be done.
Home to researchers seeking to discover novel materials and techniques for the next generation of tall wood buildings, the laboratory is itself an engineering marvel. It is a certified Passive House, the first building of its type in North America to exceed the exacting international standard.
“We pulled off something really amazing here,” says UNBC Associate Professor of Engineering Dr. Guido Wimmers. “This building has caught the attention of Passive House researchers around the world because it demonstrates how an industrial structure, constructed with wood, in Northern British Columbia’s cold climate can be a global leader in energy efficiency.”
Certified Passive House buildings use up to 90 per cent less energy for heating and cooling when compared with standard buildings and use up to 70 per cent less energy overall.
As the building owner, UNBC provided in-house expertise on the Passive House requirement and shared ideas on how to develop design and building solutions with the architectural, engineering and construction teams. Wimmers, and others in the Master of Engineering in Integrated Wood Design program, worked closely with the contractors throughout the design and construction phase of the project.
“At UNBC, we have a lot of expertise in building science, the materials the go into Passive House buildings and how we operate our buildings,” says UNBC Assistant Director of Facilities Dr. David Claus. “We’ve been able to put that all into practice on this project.”
That expertise, combined with the dedication to detail from all the project partners, resulted in impressive results.
WIRL set a new standard for air tightness, securing the best North American result of any building using the internationally recognized passive house standard. The testing protocol involves both pressurizing and depressurizing the building and measuring the number of air changes per hour that result. With a score of 0.07, WIRL surpassed the Passive House requirement by nearly a factor of 10.
The result is all the more impressive given the design requirements of the building. With a large bay door installed to facilitate the delivery of materials and a state-of-the-art dust extraction system required, there is a lot of potential for air leakage.
“The biggest challenge was the large overhead door,” Wimmers explains. “It is very difficult to find a manufacturer who can deliver a well-insulated and air-tight product.”
The big red door was sourced from Germany and the other doors and windows hail from Poland. European parts were required for those aspects of the building because Passive House manufacturing is still in its early stages in Canada.
Other components of the building were locally sourced, including the trusses used vertically in the design of the thick exterior walls.
“Using trusses as a vertical component is something unique,” Wimmers says. “I have been working in Passive Houses for more than 15 years and I have not seen any kind of technical system like this before.”
The 50-cm wide walls are rated R-80 and contain blown in mineral wool insulation. The roof is rated R-100 and required special certification from the Roofing Contractors Association of British Columba. Even the floor sits atop 20 cm of expanded polystyrene insulation.
“The entire envelope needs to be really well insulated,” Wimmers explains. “Everything has to be nicely wrapped with a warm blanket.”
Even with the air-tight design and extra insulation, the building also needs to be breathable so that any moisture that may accumulate is not trapped inside.
Wimmers and Master of Engineering program graduate Stephanie Wall produced a comparative life-cycle assessment, looking at the wood-based Passive House design of WIRL and comparing it a wood structure, built to standard building code requirements; a steel structure designed to be a Passive House; and a steel structure built to code.
The wood designs contained much less embodied energy – or energy consumed during the production of building materials and the construction itself – compared with the steel buildings. The Passive House buildings use much less energy operationally, and the wood-Passive House design scored the best overall.
“A Passive house building outperforms a code building substantially in the long run,” Wimmers says. “It’s about a third of the environmental impact compared to a code building over 60 years.”
To further reduce WIRL’s carbon footprint, the University has signed a biogas contract. By using gas recovered from agricultural facilities and landfills, UNBC is able to lessen its reliance on fossil fuels.
The Passive House design, combined with the biogas fuel, means the building is expected to produce one per cent of greenhouse gas emissions compared with a conventional building.
There’s one more benefit to the Passive House that cannot be quantified.
“In Passive House we often talk all about the low energy use,” says Claus. “But because of the ventilation systems, they are also very comfortable to live in.”